Thursday 23rd January 2025, this week’s session was very productive, and we all felt very refreshed and well into our regular flow of working – but being a good chunk into the term meant we were all feeling the pressure from the approaching regionals competition.
(And of course, we split off into our usual sub-teams for the session)
Hardware and Assembly
This was our most productive week in terms of hardware and assembly so far; with many people, who traditionally weren’t seen on the hardware side of operations, chipping in to help out. We started by attaching the wood panels to the outer parts of the wheel – unfortunately due to some miscommunication (or lack thereof) they were painted upside down and we decided it wasn’t worth the trouble to re-paint, we would rather progress and attach them regardless, if we move onto nationals we’ll consider re-painting them. However, despite how unfortunate it was, it definitely taught us an important lesson on communication! Attaching them was a quick and easy process, at one point three of us were working on individual wheels which led to some uncomfortable positions trying to screw the screws in.
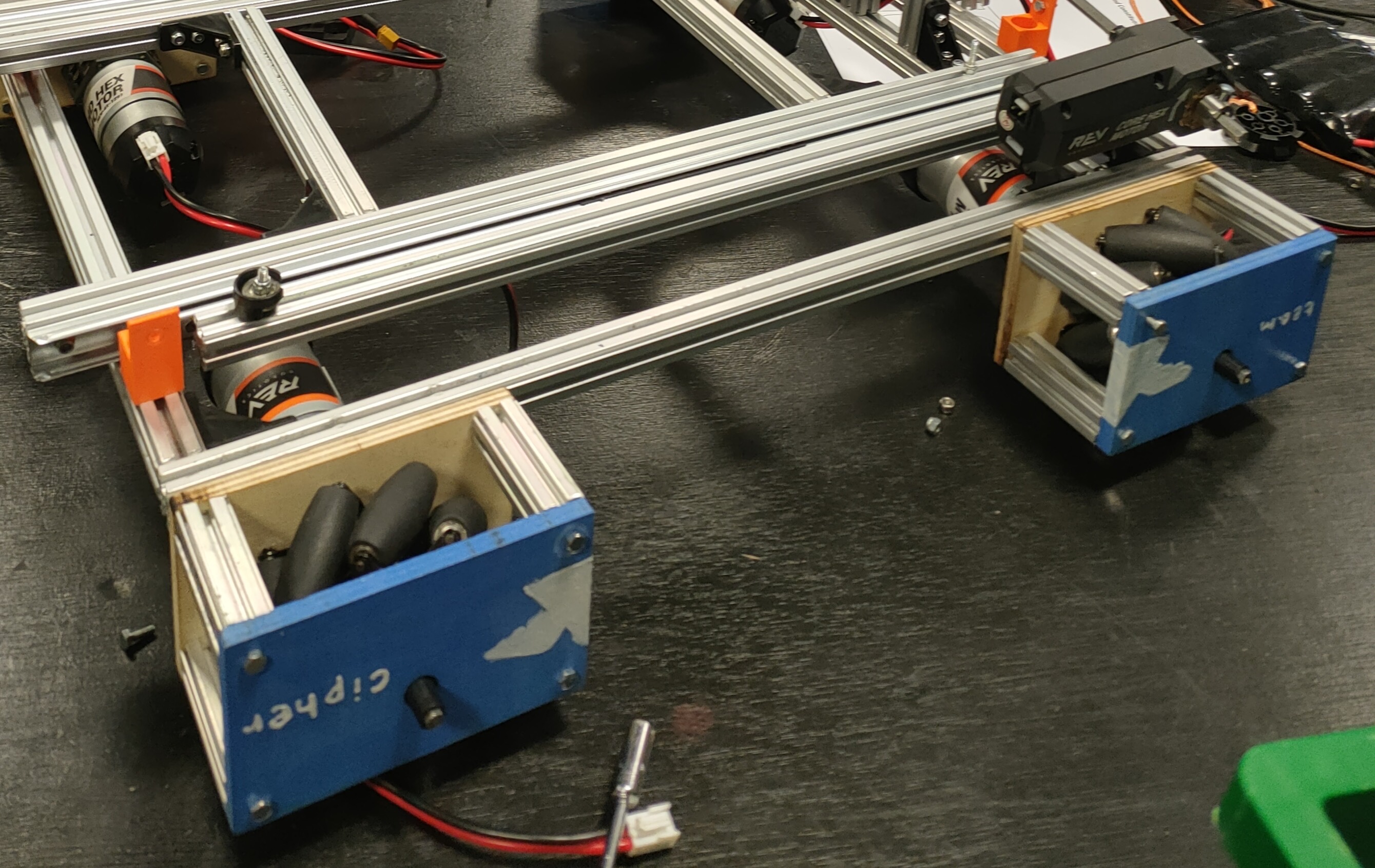
We found that the wheels were splaying out, our original plan to fix this was to attach an aluminum bar to keep it from doing so but after further consideration we felt it would be easier to simply attach a plate onto the end – but were unsure if the laser cutter would be able to cut to that size.
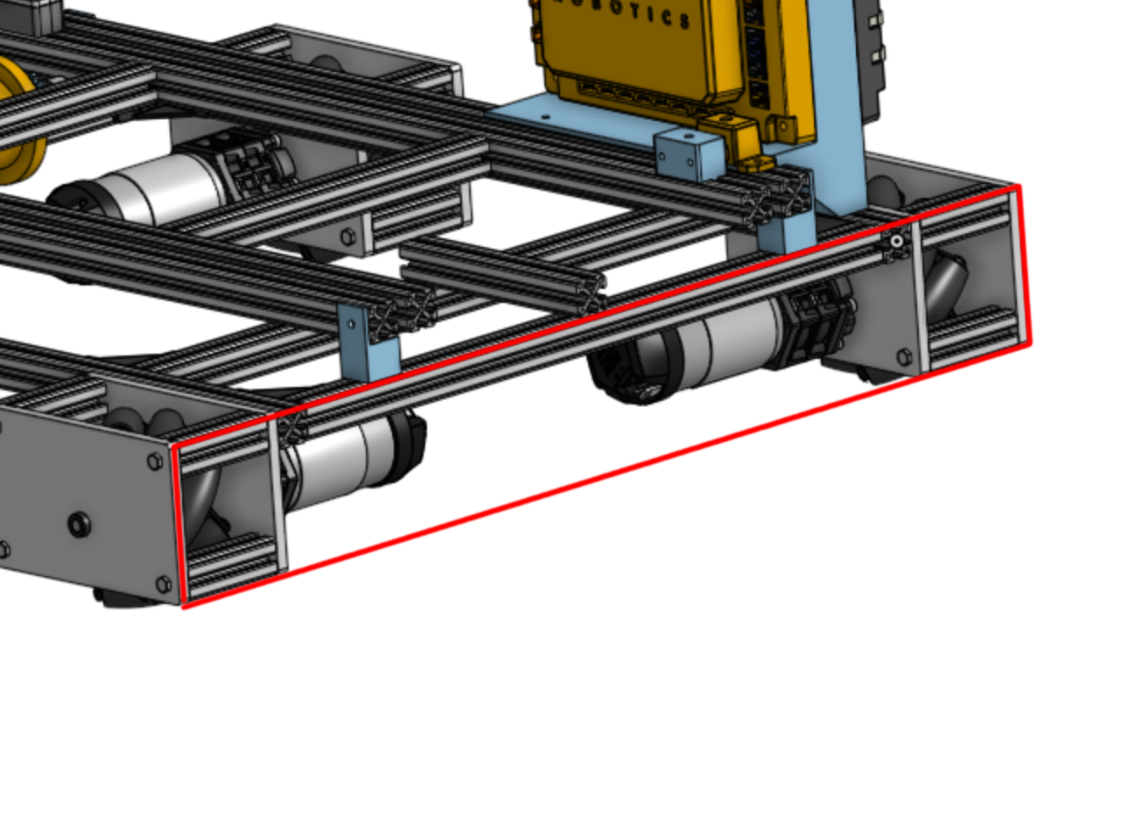
At the same time of our wheel parts attaching, we had people working on additional parts to the robot, for example the expansion hub. On top of that, this week we were prototyping an intake. Leonard, our main person for anything robot related, printed a roller that had holes to stick surgical tubing through. During and after hot gluing all the tubes in, we started to realise the tubes would likely be too flimsy to move the samples, regardless of how fast we spun it, we also noticed other problems with the intake as well. After this, we thought of changes to make to the intake, the main being to use cable ties instead of the tubing, to make it more spacious, and to use gears instead of a chain.
Outreach and Fundraising
This week we really focused in on refining the details of our upcoming Valentine’s Day bake sale. Since we only see the younger team every fortnight we wanted to work ahead of schedule and polish out the plan early so we can avoid any mishaps in the future. Together – discussing with the individuals on our teams – we agreed on who would bake, what they’ll bake and how much, we also finalised who would sell on the day. Additionally, and we sent our graphic designer (me, Emma) home with a task to create a poster for the bake sale.
Outside of Sessions
This week we also did plenty outside of the session as well (partially why this post is coming out so late)! As mentioned earlier, I was sent home with homework to design a bake sale poster, which I designed and then made a second variation of after being given advice and feedback from Shaked (thank youu, Shaked!!)
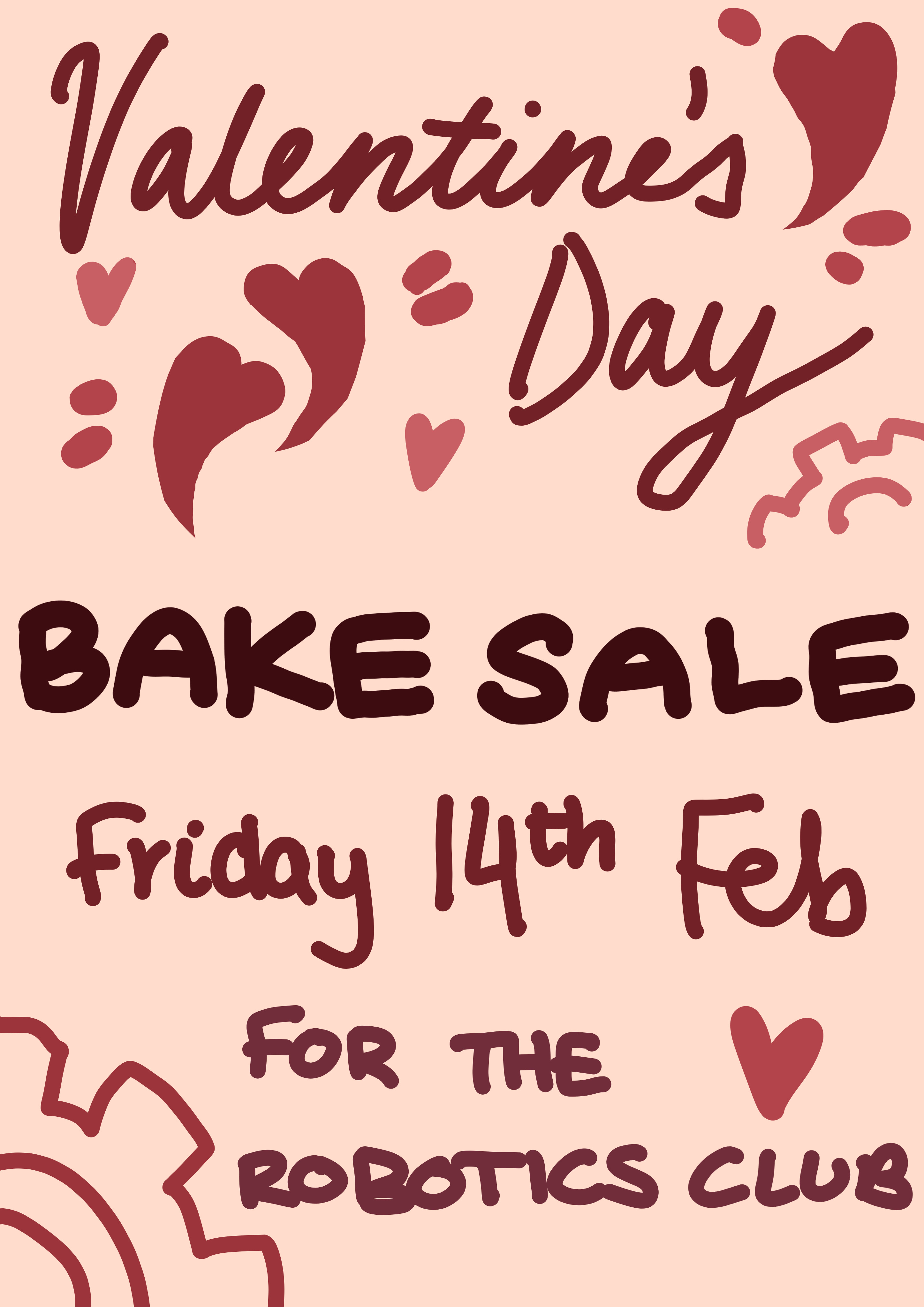
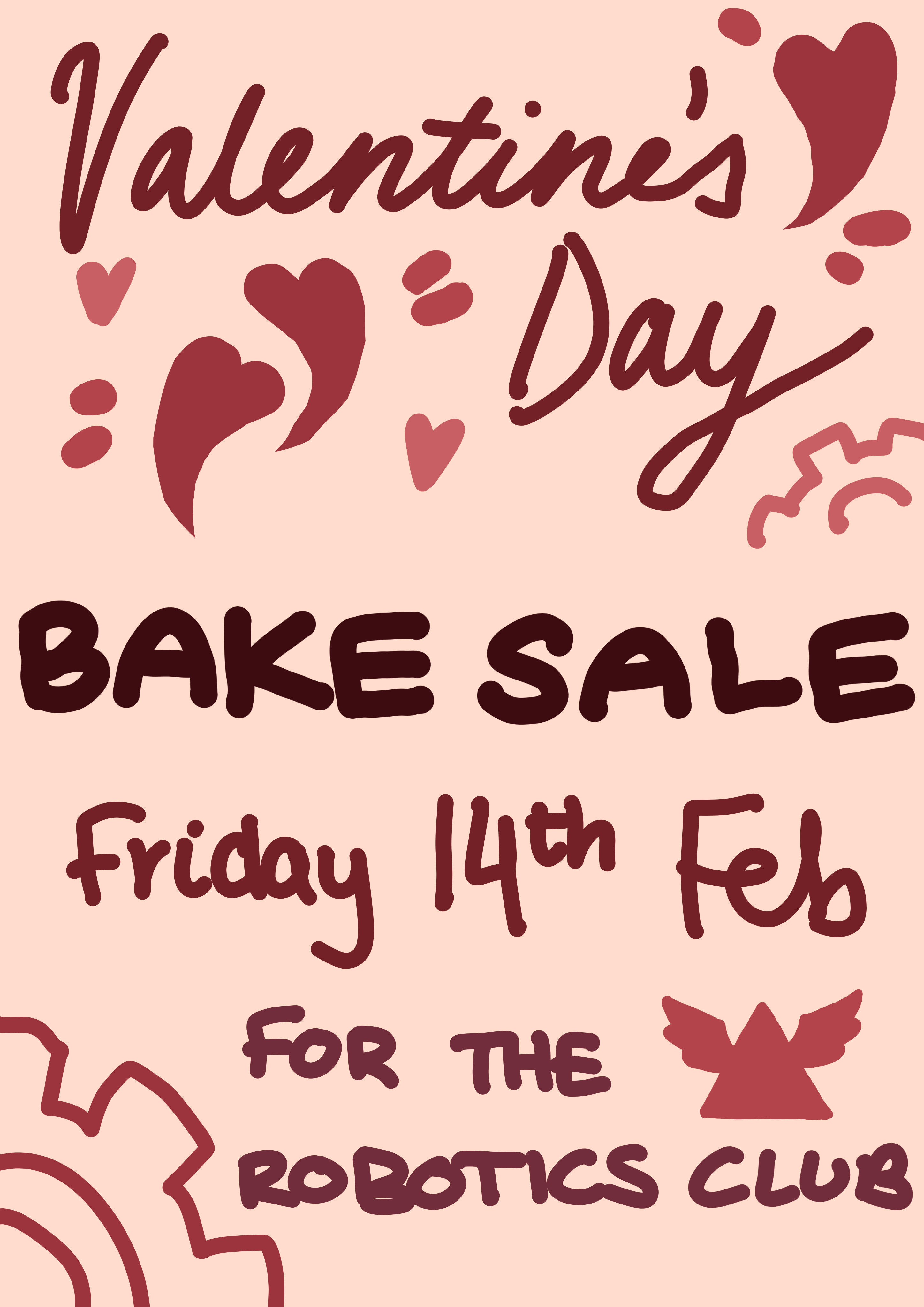
Furthermore, Leonard finalised the control layout – communicating with our drive team to ensure they’re optimal, and also did lots of 3D printing and CAD design e.g. the bucket for the samples and more. (We would be lost without you Leonard!! Massive thank you, and you have all of our respect!)